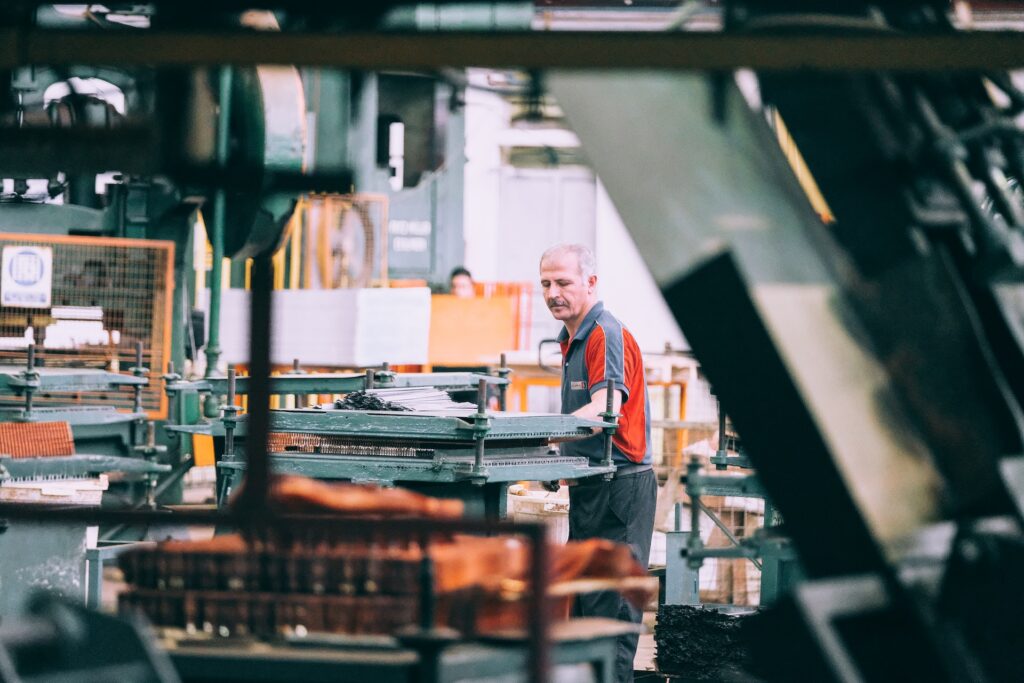
Sheet metal folding is a fundamental process in the world of metalworking and manufacturing. It allows for the creation of complex shapes, precise angles, and functional components in various industries, from automotive and construction to electronics and aerospace. The art and science of sheet metal folding involve a delicate balance of technique, machinery, and design principles. In this article, we will explore the process of sheet metal folding, its applications, tools and equipment involved, and the innovative techniques shaping its future.
I. Understanding Sheet Metal Folding
Sheet metal folding, also known as press braking or brake forming, is a process in which a flat sheet of metal is bent along one or more axes to create a desired shape or component. This process can be applied to a variety of metals, including steel, aluminum, copper, and stainless steel, and is employed for both decorative and structural purposes. The primary objective of sheet metal folding is to transform a flat sheet into a three-dimensional object with precise angles and dimensions.
II. Applications of Sheet Metal Folding
- Architectural Metalwork: Sheet metal folding is commonly used in architectural design to create decorative elements, facades, and structural components for buildings and bridges.
- Automotive Industry: In the automotive sector, sheet metal folding is vital for manufacturing vehicle body panels, chassis components, and exhaust systems.
- Aerospace Engineering: The aerospace industry relies on sheet metal folding to fabricate lightweight and high-strength components for aircraft and spacecraft.
- Electronics: Sheet metal folding is used to produce enclosures, brackets, and chassis for electronic devices, ensuring precision and durability.
- Construction: Construction applications include the fabrication of structural components like beams, columns, and trusses, as well as decorative elements for architectural projects.
- HVAC Systems: Sheet metal folding is integral in the production of heating, ventilation, and air conditioning (HVAC) systems, particularly for ductwork and components.
III. The Sheet Metal Folding Process
The sheet metal folding process involves several key steps, from material preparation to the final product:
- Material Selection: The choice of sheet metal material and its thickness depends on the specific requirements of the project.
- Material Cutting: The metal sheet is cut to the required size, often using shearing or laser cutting techniques.
- Tool Selection: Depending on the desired bend angle, different tooling is selected. This includes dies, punches, and press brakes.
- Clamping: The metal sheet is clamped between the die and punch, with the punch exerting force to create the bend.
- Bending: The bending process is carried out, resulting in the sheet metal taking on the desired shape.
- Quality Inspection: The final product is inspected for accuracy and adherence to design specifications.
IV. Sheet Metal Folding Equipment
Sheet metal folding is made possible by specialized machinery and equipment designed for precision and efficiency. The key equipment used in the process includes:
- Press Brake: The press brake is the central tool in sheet metal folding. It exerts force on the metal sheet to create bends. Modern press brakes are often equipped with CNC (Computer Numerical Control) systems for high precision.
- Dies and Punches: Dies and punches are the tooling components that shape the metal. They come in various shapes and sizes to achieve different bend angles and radii.
- Back Gauge: The back gauge is used to position the metal sheet accurately before bending, ensuring consistent results.
- Finger Brake: A finger brake is a specialized press brake used for making small, precise bends, typically with a maximum capacity of 16 or 18-gauge sheet metal.
V. Techniques in Sheet Metal Folding
The world of sheet metal folding is not static; it is continually evolving with new techniques and innovations. Some notable advancements and trends include:
- 3D Sheet Metal Folding: Traditionally, sheet metal folding is carried out along one axis. However, 3D sheet metal folding technology allows for complex shapes to be formed by folding along multiple axes. This opens up new design possibilities in industries like aerospace and architecture.
- Precision Tooling: Advancements in tooling technology, including the development of precision dies and punches, allow for more intricate and accurate bends, reducing the need for post-processing.
- Automated Press Brakes: The integration of automation and robotics into press brakes is enhancing productivity and consistency. Automated systems can handle repetitive tasks and maintain precision over long production runs.
- Hybrid Manufacturing: The combination of sheet metal folding with additive manufacturing (3D printing) is gaining traction. This approach allows for the creation of components with highly complex geometries and the integration of multiple materials.
VI. Challenges and Considerations
While sheet metal folding is a highly versatile and effective process, it comes with certain challenges and considerations:
- Material Limitations: Not all materials are suitable for sheet metal folding. Some materials may be too brittle, while others may be too thick for conventional press brakes.
- Tolerances: Achieving precise tolerances and avoiding defects like springback (the tendency of metal to return to its original shape) requires expertise and tooling adjustments.
- Design Complexity: Complex designs with multiple bends and curves may require specialized tooling and machinery, adding to the complexity and cost of production.
- Material Thickness: The thickness of the sheet metal influences the bending process. Thicker materials may require higher tonnage press brakes, while thinner materials may require more careful handling to prevent distortion.
Sheet metal folding is a dynamic and indispensable process in the world of manufacturing and design. From architectural marvels to the creation of intricate components in industries like aerospace and automotive, it plays a pivotal role in shaping our world. As technology continues to advance and new techniques are developed, the future of sheet metal folding promises even greater precision, versatility, and innovation, further establishing its importance in the metalworking industry. Whether it’s a functional component or a work of art, sheet metal folding remains an essential skill and a transformative process in modern fabrication.